BLACK CLAWSON LTD.



THERMOPLANISHER – GLOSS CALENDER
It is important for the board manufacturer to consider the surface of his product for good appearance and printing characteristics in addition to functional properties.
For improved gloss of the finished board, Black Clawson Ltd. offer the Thermoplanisher Gloss Calender. This machine is designed to improve the surface finish of coated and uncoated paper and board without appreciable loss of bulk, by the application of heat and pressure. To produce a smooth, flat glossy surface lies in the thermoplastic flow achieved at the surface of the web contacting the planishing roll when nipped with the rubber covered pressure roll.
The planishing roll itself must have a very smooth surface since it produces the final smooth result desired. It also must be heated. The Black Clawson Thermoplanisher uses either steam or hot oil to produce the heat required in the Planishing Roll.
The degree of finish obtained is dependant on a number of factors.
-
Contact time of the web surface with the planishing roll
-
Finish of the base stock to be planished
-
Percentage moisture in the web and in the coating
-
Type of binder used in the coating
-
Percentage total binder in the coating
-
Types of pigment in the coating
-
Total coat weight on the sheet
-
Temperature of the planishing roll
-
Pressure of the planishing nip and nip width
-
Characteristics of the rubber covering on the pressure roll
Final results obtained depend on a combination of all the above variables.
​
​
​
​
​
​
​
​
​
​
​
​
​
​
​
​
​
​
​
​
​
​
​
​
​
Fig 1. Two Nip Thermoplanisher
Features of the Black Clawson Two Nip Thermoplanisher can be described as follows.
-
The Hot Roll is chrome plated, ground and polished to a mirror finish. The roll can be either steam heated or hot oil heated. The temperature range for this roll is between 90º and 200ºC.
-
The hot roll is mounted to the frames in a fixed position in heavy duty anti friction bearings, with housings designed to allow oil circulation for lubrication and cooling.
-
The Hot Roll is driven by an electric drive
-
Two rubber covered pressure rolls are supplied. They can be run together or independently allowing for one roll to be reground whilst still using the other in the machine.
-
The pressure rolls are mounted to pivoting arms and also use heavy duty anti friction bearings, with housings designed to allow oil circulation for lubrication and cooling
-
The pressure rolls are driven by separate electric drives.
-
Pressure roll movement is controlled by a dual hydraulic loading system. A low pressure high volume pump provides the movement. At the moment of contact a high pressure low volume pump supplies the nip pressure. The high nip pressure required is produced using high pressure hydraulic cylinders. Controlled pressures up to a maximum of 150kg/cm can be achieved.
-
Rubber covered rolls are water cooled to maintain the rubber bond to the core under the high pressure and temperature conditions.
-
A doctor is provided to operate in close proximity to the surface of the Hot roll to prevent wrap up should a web break occur. The doctor is only engaged on web break.
-
Web rolls are provided within the framework of the thermoplanisher to ensure proper lead in and out of the planishing nips. These rolls are easily adjustable in the horizontal plane.
-
An optional hot roll traversing buffing unit can be supplied for cleaning of the Hot roll if required.
Click here for Board Coating document
Typical Machine Photos
(Click to Enlarge)
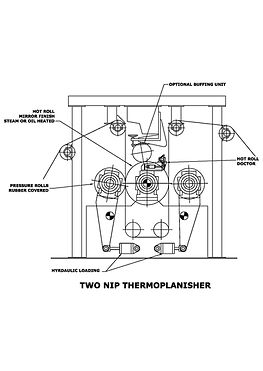

Themoplanisher Web Roll Adjustment
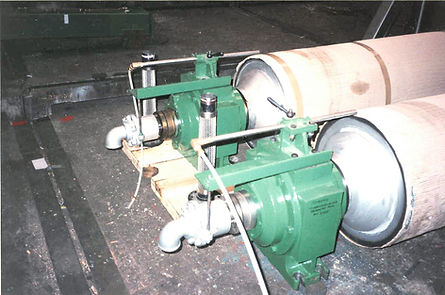
Thermoplanisher Pressure Rolls & Bearings

Thermoplanisher Hydraulic Loading

Thermoplanisher Hot Roll Assembly

Thermoplanisher on Assembly